Kalıp Tasarımı Çiziminde Dikkat Edilmesi Gereken Hususlar
Kalıp Tasarımı Çiziminde Dikkat Edilmesi Gereken Hususlar
Germe kalıpları, toplamın çok büyük bir bölümünü oluşturur. presleme endüstri ölür. Ortak kaplarımız, motor üzerindeki kabuk ve hemen hemen çoğu üründe az ya da çok gerdirilmesi gereken ürünler vardır. Kalıbın tasarımı, geleneksel algoritmaya göre hesaplanabileceğini söylemek değildir. Değişkenlerle dolu çok fazla süreç var, özellikle de dönmeyen bazı cisimlerin esnetilmesi, ki bu yasak. Çünkü çekme kalıbının tasarımında çekme katsayısı, malzemenin sınırına ulaşıp ulaşmadığı, yay kuvvetinin kararı, çekme yönü, yukarı mı aşağı mı olduğu gibi çok fazla faktör göz önünde bulundurulur. , genellikle olamaz Tek seferlik kalıplama, istenen sonucu elde etmek için birçok deneme gerektirir ve bazen kalıp hurdaya ayrılabilir. Bu nedenle, pratikte birikmiş deneyim, çizim kalıbının tasarımına çok yardımcı olur. Ayrıca kesme malzemesinin boyutu da kalıbın tamamının deneme üretiminde önemli bir rol oynar. Bu nedenle çoğu zaman, bazı düzensiz derin çekilmiş parçalar tasarladığımızda, kalıp tasarım aşamasında genellikle boş bir adım bırakırız. |
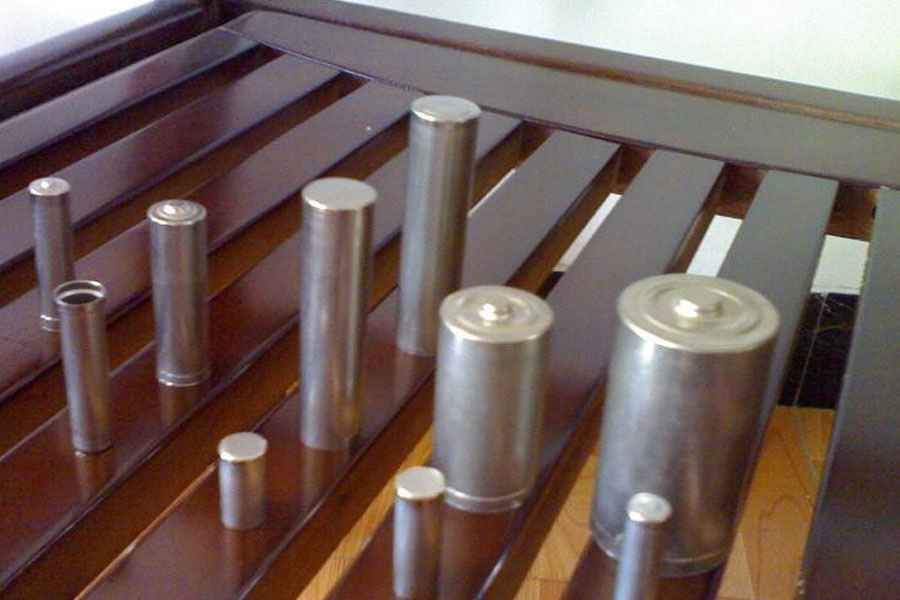
Germe Malzemesi:
Müşterinin malzeme gereksinimleri çok zorlayıcı olmadığında ve tekrarlanan kalıp denemeleri gereksinimleri karşılayamadığında, iyi çekme özelliklerine sahip bir malzemeye geçebilir ve tekrar deneyebilirsiniz. İyi bir malzeme başarının yarısıdır. Germe için, göz ardı edilmemelidir. Çekme için soğuk haddelenmiş ince çelik saclar esas olarak 08Al, 08, 08F, 10, 15 ve 20 çelikleri içerir. En büyük miktar, çerçeveli çelik ve öldürülmüş çelik olarak ayrılan 08 çeliktir. Kenarlı çelik fiyatı düşüktür ve iyi yüzey kalitesine sahiptir. Ayrışma daha ciddidir ve "gerilme yaşlanması" eğilimine sahiptir. Yüksek damgalama performansı ve görünüm gereksinimleri gerektiren parçalar için uygun değildir. Öldürülmüş çelik, tek tip performansla ancak daha yüksek fiyatla daha iyidir. Temsili marka, alüminyumla öldürülmüş çelik 08Al'dir. Yabancı çelik, Japon SPCC-SD derin çekme çeliğini kullanmıştır ve çekme özellikleri 08Al'den daha iyidir. Müşterinin malzeme gereksinimleri çok zorlayıcı olmadığında ve tekrarlanan kalıp denemeleri gereksinimleri karşılayamadığında, başka bir malzemeye geçebilir ve tekrar deneyebilirler.
Kalıp Yüzeyinin Bitirilmesi.
Derin çekme yapılırken, kalıbın iki tarafı ve boşluk tutucu yeterince taşlanmaz, özellikle paslanmaz çelik levhalar ve alüminyum levhalar çizilirken, ağır durumlarda çekme kırılmalarına yol açabilen çekme izlerinin oluşması daha olasıdır.
Boş Boyut Tayini:
Daha fazla kırışıklık ve daha az çatlak prensibimizdir. Boş konumlandırma tasarımı doğru olmalıdır. Basit şekle sahip dönen gövde çekme parçasının boş çapı inceltilmez. Malzeme kalınlığı değişse de temelde orijinal kalınlığa çok benzer. Yakınlık, işlenmemiş parçanın alanı ile gerilmiş parçanın (eğer kırpma eklenecekse) alanının eşit olması ilkesine göre hesaplanabilir. Bununla birlikte, gerilmiş parçaların şekli ve işlemi genellikle karmaşıktır ve bazen inceltilip gerdirilmeleri gerekir. Katlanmamış malzemeyi hesaplayabilen birçok üç boyutlu yazılım olmasına rağmen, doğruluğu %100 gereksinimlerini karşılayamaz.
Çözüm: örnek. Bir ürün birden fazla işlemden geçmelidir ve ilk işlem genellikle bir körleme işlemidir. Her şeyden önce, körleme kalıbının toplam boyutunu belirlemek için, katlanmamış malzemenin hesaplanmasını yapmak ve boşluğun şekli ve boyutu hakkında genel bir anlayışa sahip olmak gerekir. Kalıp tasarımı tamamlandıktan sonra körleme kalıbının dışbükey ve içbükey kalıp boyutunu işlemeyin. Boşluğu işlemek için önce tel kesmeyi kullanın (boşluk daha büyük olduğunda, bir freze makinesiyle frezelenebilir ve ardından sıkıştırılabilir). Müteakip germe işleminde tekrarlanan deneylerden sonra, boşluğun boyutu nihayet belirlenir ve ardından boşluk kalıbının dışbükey ve içbükey kalıpları işlenir.
Deneyim 2: İşlemi tersine çevirin, önce çizim kalıbını deneyin ve ardından yarı çaba olan boşluğun boşluk kenar boyutunu işleyin.
streç katsayısı
Germe katsayısı, germe işleminin hesaplanmasında ana işlem parametrelerinden biridir ve genellikle germe sırasını ve sayısını belirlemek için kullanılır. Malzeme özellikleri, malzemenin nispi kalınlığı, germe yöntemi (boş tutucunun olup olmadığına atıfta bulunarak), germe süreleri, germe hızı, dışbükey ve içbükey kalıp köşe yarıçapı, yağlama vb. dahil olmak üzere germe katsayısı m'yi etkileyen birçok faktör vardır. Çekme katsayısı m'nin hesaplanması ve seçim ilkeleri, çeşitli damgalama kılavuzlarında tanıtılan kilit noktalardır. Hesaplama, tablo arama, hesaplama gibi bir çok yöntem var ve ben de kitabına göre seçiyorum. Yeni bir şey yok. Lütfen kitabı okuyun. .
Deneyim 3: Malzemenin nispi kalınlığı, gerdirme yöntemi (boş tutucu olup olmadığına atıfta bulunarak) ve gerdirme sayısı, kalıbı tamir ederken ayarlamak kolay değildir. Dikkatli olmalısınız!! Gerilme katsayısı m seçilirken bir meslektaş bulmak en iyisidir.
İşleme yağı seçimi çok önemlidir. Yağlama yağının uygun olup olmadığını anlamanın yolu, ürün kalıptan çıkarıldığında, eğer ürün sıcaklığı el değmeyecek kadar yüksekse, yağlama yağı seçimi ve yağlama yöntemi yeniden gözden geçirilmeli ve yağlama yöntemi tekrar gözden geçirilmelidir. boşluğa yağlama yağı uygulanmalıdır. , Veya kağıda bir film poşeti koyun.
Deneyim 4: Çekme çatlaması ile karşılaştığınızda, kalıba yağlama yağı uygulayın (dışbükey kalıba uygulamayın) ve iş parçası kalıbın yanında 0.013-0.018 mm plastik film ile kaplanır.
İş Parçası Isıl İşlemi
Tavsiye edilmese de yine de söylemek gerekir ki, germe işlemi sırasında iş parçasının soğuk plastik deformasyonu nedeniyle plastikliğini azaltan, deformasyon direncini ve sertliğini artıran soğuk iş sertleşmesi meydana gelir ve kalıp tasarımı mantıksızdır. Metali yumuşatmak ve plastisiteyi geri kazandırmak için ara tavlama.
Not: Genel işlemde ara tavlama gerekli değildir. Sonuçta, maliyeti artırmak gerekiyor. İşlemi artırmak ve tavlamayı artırmak arasında seçim yapmalı ve dikkatli kullanmalısınız! Tavlama genellikle düşük sıcaklıkta tavlamayı, yani yeniden kristalleştirme tavını benimser. Tavlama yaparken dikkat edilmesi gereken iki şey vardır: dekarburizasyon ve oksidasyon. Burada esas olarak oksidasyon hakkında konuşuyoruz. İş parçası oksitlendikten sonra oksit ölçeği var,
İki dezavantajı vardır: iş parçasının etkin kalınlığının incelmesi ve kalıp aşınmasının artması. Şirket koşullarının uygun olmadığı durumlarda genellikle normal tavlama yapılır. Oksit tortusu oluşumunu azaltmak için tavlama sırasında fırın mümkün olduğunca doldurulmalıdır. Ayrıca toprak yöntemlerini de kullandım:
- - Az sayıda iş parçası olduğunda diğer iş parçalarıyla karıştırılabilir (ön koşul: tavlama işlemi parametreleri temelde aynı olmalıdır)
- - İş parçasını demir kutuya koyun ve fırına kaynak yapın. Oksit tortusunu ortadan kaldırmak için tavlama sonrası duruma göre dekapaj işlemi yapılmalıdır. Firma şartları müsait olduğunda azot fırını tavlama yani parlak tavlama kullanılabilir. Yakından bakmazsanız, renk tavlama öncesi ile hemen hemen aynıdır.
Deneyim 5: Güçlü soğuk işleme sertleşmesine sahip metallerle uğraşırken veya test kalıbında çatlamanın başka bir yolu olmadığında ara tavlama işlemi ekleyin.
Eklenecek Birkaç Nokta
- 1. Ürün çizimindeki boyut, dış boyutun veya iç boşluk boyutunun garanti edilip edilmediğini netleştirmek için mümkün olduğunca bir tarafta işaretlenmelidir ve iç ve dış boyutlar aynı anda işaretlenemez. Başkaları tarafından sağlanan çizimlerin bu tür sorunları varsa, onlarla iletilmelidir. Birleşebilirlerse, birleştirilmeleri gerekir. Birleştirilemezlerse, iş parçası ile diğer parçalar arasındaki montaj ilişkisini bilmelidirler.
- 2. Son işlem için, iş parçasının boyutu dışarıdadır, kalıp anadır, zımba boyutunun küçültülmesiyle boşluk elde edilir; iş parçasının boyutu içeride, zımba ana ve kalıbın boyutu artırılarak boşluk elde edilir;
- 3. Dışbükey ve içbükey kalıpların köşe yarıçapı, sonraki kalıp onarımına kolaylık sağlamak için mümkün olduğunca küçük tasarlanmalıdır.
- 4. İş parçasının çatlama nedenini değerlendirirken buna başvurabilirsiniz: düşük malzeme kalitesinden kaynaklanan çatlaklar çoğunlukla tırtıklı veya düzensiz şekillerdedir ve işlemden ve kalıptan kaynaklanan çatlaklar genellikle nispeten düzgündür.
- 5. "Daha fazla kırışıklık, daha az çatlak" Bu prensibe göre malzemenin akışını ayarlayın. Yöntemler, boş tutucunun basıncını ayarlamayı, çekme boncukunu arttırmayı, içbükey ve dışbükey kalıbın köşe yarıçapını kırpmayı ve iş parçası üzerindeki işlem açıklığını kesmeyi içerir.
- 6. Aşınma direncini sağlamak ve çekme çiziklerini önlemek için içbükey-dışbükey kalıp tutucu halka su verilmelidir. Ayrıca sert kaplamalı olabilir, yüzey TD işlemi de kullanılabilir ve gerektiğinde içbükey ve dışbükey kalıplar olarak tungsten çelik kullanılabilir.
Bu makaleye bağlantı: Kalıp Tasarımı Çiziminde Dikkat Edilmesi Gereken Hususlar
Yeniden Baskı Bildirimi: Özel bir talimat yoksa, bu sitedeki tüm makaleler orijinaldir. Lütfen yeniden basılacak kaynağı belirtin:https://www.cncmachingptj.com/,teşekkürler!
PTJ CNC atölyesi, metal ve plastikten mükemmel mekanik özelliklere, hassasiyete ve tekrarlanabilirliğe sahip parçalar üretir. 5 eksenli CNC freze mevcuttur.Yüksek sıcaklıkta alaşımın işlenmesi aralık dahil inconel işleme,monel işleme,Geek Ascology işleme,Sazan 49 işleme,Hastelloy işleme,Nitronic-60 işleme,Hymu 80 işleme,Takım Çeliği işleme,vb.,. Havacılık uygulamaları için idealdir.CNC'de işleme metal ve plastikten mükemmel mekanik özelliklere, hassasiyete ve tekrarlanabilirliğe sahip parçalar üretir. 3 eksenli ve 5 eksenli CNC freze mevcuttur. Hedefinize ulaşmanıza yardımcı olacak en uygun maliyetli hizmetleri sunmak için sizinle birlikte strateji oluşturacağız, Bize Hoş Geldiniz ( satış@pintejin.com ) doğrudan yeni projeniz için.
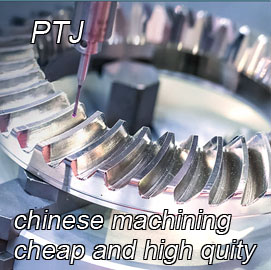
- 5 Eksen İşleme
- Cnc Frezeleme
- Cnc Tornalama
- İşleme Endüstrileri
- Işleme süreci
- Yüzey İşlem
- Metal İşleme
- Plastik İşleme
- Toz Metalurji Kalıbı
- Döküm Döküm
- Parça Galerisi
- Oto Metal Parçaları
- Makine parçaları
- LED Soğutucu
- Yapı Parçaları
- Mobil Parçalar
- Tıbbi Parçalar
- Elektronik parçalar
- Özel İşleme
- Bisiklet Parçaları
- Alüminyum İşleme
- titanyum işleme
- Paslanmaz Çelik İşleme
- Bakır İşleme
- Pirinç İşleme
- Süper Alaşımlı İşleme
- Peek İşleme
- UHMW İşleme
- Unilate İşleme
- PA6 İşleme
- PPS İşleme
- Teflon İşleme
- İnkonel İşleme
- Takım Çeliği İşleme
- Daha Fazla Malzeme