Vakum indüksiyon eritme teknolojisinin gelişimi ve trendi
Modern endüstriyel teknolojinin hızlı gelişimi ile, insanların mekanik parçaların kullanımına yönelik gereksinimleri giderek artıyor ve daha şiddetli kullanım ortamı, yüksek sıcaklık dayanımı, aşınma direnci, yorulma direnci ve metal malzemelerin diğer özellikleri için daha yüksek gereksinimleri ortaya koyuyor. .
Bazı özel metaller veya alaşım malzemeleri için, ister erken aşamadaki Ar-Ge testi isterse sonraki aşama seri üretim olsun ve kullanıma sunulsun, yüksek performanslı metal alaşımlı malzemelerin araştırılması veya elde edilmesi, metal eritme ekipmanı, yüzey ısıl işlem ekipmanı vb. desteğini gerektirir. birçok özel ısıtma veya ergitme yöntemi, indüksiyon ısıtma teknolojisi, metal malzemeleri eritmek ve hazırlamak veya hayati bir rol oynayan belirli bir işlemde malzemeleri sinterlemek ve ısıl işlem yapmak için kullanılır.
Bu makale, vakumlu indüksiyon ergitme teknolojisinin geliştirme sürecini ve farklı durumlarda indüksiyon ergitme teknolojisinin uygulanmasını tanıtmaktadır. Farklı vakumlu indüksiyon ocağı tiplerinin yapısına göre avantaj ve dezavantajlarını karşılaştırın. Vakum indüksiyon fırınlarının gelecekteki gelişim yönünü dört gözle beklemek, gelişme eğilimini açıklamaktadır. Vakumlu indüksiyon fırınlarının gelişimi ve ilerlemesi, esas olarak ekipmanın genel yapısının kademeli olarak iyileştirilmesine, giderek belirginleşen modülerleştirme eğilimine ve daha akıllı kontrol sistemine yansır.
1. Vakum indüksiyon eritme teknolojisi
1.1 İlke
__kindeditor_temp_url__İndüksiyonla ısıtma teknolojisi genellikle, vakum koşullarında ısıtma amacına ulaşmak için daha iyi manyetik duyarlılığa sahip malzemeler için endüksiyon akımı elde etmek için elektromanyetik indüksiyon prensibini kullanan bir teknolojiyi ifade eder. Elektrik akımı, metal malzemeyi çevreleyen elektromanyetik bobinden belirli bir frekansta geçer. Değişen elektrik akımı, metalde indüklenen bir akıma neden olan ve malzemeyi ısıtmak için büyük miktarda ısı üreten indüklenmiş bir manyetik alan oluşturur. Isı nispeten düşük olduğunda, vakum indüksiyonlu ısıl işlem ve diğer işlemlerde kullanılabilir. Isı yüksek olduğunda, üretilen ısı metali eritmek için yeterlidir ve metal veya alaşımlı malzemelerin hazırlanmasında kullanılır.
1.2, uygulama
1.2.1, vakum indüksiyon eritme
Vakum indüksiyonlu eritme teknolojisi şu anda metal malzemeleri ısıtmak için en verimli, en hızlı, düşük tüketimli, enerji tasarrufu sağlayan ve çevre dostu endüksiyonlu ısıtma teknolojisidir. Bu teknoloji esas olarak indüksiyon eritme fırınlarında ve diğer ekipmanlarda uygulanmaktadır ve çok çeşitli uygulamalara sahiptir. Katı metal hammaddeler, bir bobin ile sarılmış bir potaya yerleştirilir. Akım endüksiyon bobininden geçtiğinde, indüklenen bir elektromotor kuvveti üretilir ve metal yükün içinde bir girdap akımı üretilir. Mevcut ısı, metal yükünün ısı yayılım oranından daha büyük olduğunda, ısı giderek daha fazla birikir. Belirli bir seviyeye ulaştığında, metal eritme amacına ulaşmak için metal katı halden sıvı hale erir. Bu işlemde tüm işlem vakum ortamında gerçekleştiği için metal içindeki gaz safsızlıklarının giderilmesinde fayda vardır ve elde edilen metal alaşımlı malzeme daha saftır. Aynı zamanda, eritme işlemi sırasında, vakum ortamının kontrolü ve indüksiyonla ısıtma yoluyla, eritme sıcaklığı ayarlanabilir ve rafine etme amacına ulaşmak için alaşım metali zamanında tamamlanabilir. Eritme işlemi sırasında, indüksiyon eritme teknolojisinin özelliklerinden dolayı, pota içindeki sıvı metal malzeme, bileşimi daha düzgün hale getirmek için elektromanyetik kuvvetin etkileşimi nedeniyle otomatik olarak karıştırılabilir. Bu aynı zamanda indüksiyon eritme teknolojisinin önemli bir avantajıdır.
Geleneksel ergitme ile karşılaştırıldığında, vakumlu indüksiyon ergitme, enerji tasarrufu, çevre koruma, işçiler için iyi çalışma ortamı ve düşük emek yoğunluğu nedeniyle büyük avantajlara sahiptir. İndüksiyon eritme teknolojisini kullanarak, nihai alaşım malzemesi daha az safsızlıktır ve eklenen alaşımın oranı daha uygundur, bu da malzemenin özellikleri için işlemin gereksinimlerini daha iyi karşılayabilir.
Vakum indüksiyon ergitme teknolojisi, deneysel araştırmalar için birkaç kilogramlık indüksiyon fırınlarından fiili üretim için onlarca ton kapasiteli büyük ölçekli indüksiyon fırınlarına kadar geniş bir ölçekte kullanılmıştır. Basit çalışma teknolojisi nedeniyle, eritme işleminin kontrolü kolaydır ve erime sıcaklığı hızlıdır. , Eritilmiş metal, tek tip bileşimin avantajlarına sahiptir ve büyük uygulama beklentilerine sahiptir ve son yıllarda hızla geliştirilmiştir.
1.2.2, vakumlu indüksiyon sinterleme
Vakum sinterleme, metal, alaşım veya metal bileşik tozunun, vakum derecesi (10-10-3Pa) olan bir ortamda erime noktasının altındaki bir sıcaklıkta metal ürünlere ve metal boşluklara sinterlenmesi anlamına gelir. Vakum koşulları altında sinterleme, metal ve gaz arasında reaksiyon yoktur ve adsorbe edilen gazın etkisi yoktur. Yoğunlaştırma etkisi sadece iyi olmakla kalmaz, aynı zamanda sinterleme sıcaklığını düşürerek arıtma ve azaltma rolü de oynayabilir ve oda sıcaklığında sinterleme oranı 100 ℃ ~ 150 ℃ azaltılabilir, Enerji tüketiminden tasarruf edin, sinterleme fırınının ömrü ve yüksek kaliteli ürünler elde edilir.
Bazı malzemeler için, atomların ısıtma yoluyla transferi yoluyla parçacıklar arasındaki bağın gerçekleştirilmesi gerekir ve indüksiyon sinterleme teknolojisi bu süreçte ısıtma rolü oynar. Vakum indüksiyon sinterlemenin avantajı, vakum koşulları altında atmosferdeki zararlı maddelerin (su buharı, oksijen, nitrojen ve diğer safsızlıklar) azaltılmasına yardımcı olması ve dekarburizasyon, nitrürleme, karbonlama, indirgeme ve oksidasyon gibi bir dizi reaksiyondan kaçınmasıdır. . İşlem sırasında gözeneklerdeki gaz miktarı azalır ve gaz moleküllerinin kimyasal reaksiyonu azalır. Aynı zamanda, malzemenin yüzeyindeki oksit filmi, malzeme sıvı fazda görünmeden önce çıkarılır, böylece malzeme eridiğinde ve yapıştırıldığında malzeme daha yoğun bir şekilde bağlanır ve aşınma direnci iyileştirilir. kuvvet. Ayrıca vakumlu indüksiyon sinterlemenin de ürün maliyetlerini düşürmede belirli bir etkisi vardır.
Vakum ortamında gaz içeriği nispeten düşük olduğundan, ısının taşınımı ve iletimi göz ardı edilebilir. Isı, esas olarak ısıtma bileşeninden malzemenin yüzeyine radyasyon şeklinde aktarılır. Seçim, spesifik sinterleme sıcaklığına ve malzemenin fiziksel ve kimyasal özelliklerine dayanmaktadır. Uygun ısıtma bileşenleri de çok önemlidir. Vakum dirençli ısıtma ile karşılaştırıldığında, indüksiyon sinterleme, belirli bir dereceye kadar dirençli ısıtma kullanan vakumlu fırınların yüksek sıcaklık yalıtım problemini önleyen ara frekanslı güç ısıtmasını benimser.
Şu anda, indüksiyon sinterleme teknolojisi esas olarak çelik ve metalurji alanlarında kullanılmaktadır. Ayrıca, özel seramik malzemeler üzerinde, indüksiyon sinterleme katı parçacıkların bağlanmasını geliştirir, kristal tanelerin büyümesine yardımcı olur, boşlukları sıkıştırır ve ardından yoğun polikristalin sinterlenmiş gövdeler oluşturmak için yoğunluğu arttırır. İndüksiyon sinterleme teknolojisi, yeni malzemelerin araştırılmasında da daha yaygın olarak kullanılmaktadır.
1.2.3, vakum indüksiyonlu ısıl işlem
Şu anda, esas olarak indüksiyonla sertleştirme teknolojisine odaklanan daha fazla indüksiyonlu ısıl işlem teknolojisi olmalıdır. İş parçasını indüktöre (bobin) koyun, indüktörden belirli bir frekansta alternatif bir akım geçtiğinde, etrafında alternatif bir manyetik alan üretilecektir. Alternatif manyetik alanın elektromanyetik indüksiyonu, iş parçasında kapalı bir girdap akımı üretir. Deri etkisinden dolayı, yani indüklenen akımın iş parçasının kesiti üzerindeki dağılımı çok düzensizdir, iş parçasının yüzeyindeki akım yoğunluğu çok yüksektir ve içe doğru giderek azalır.
İş parçasının yüzeyindeki yüksek yoğunluklu akımın elektrik enerjisi, yüzeyin sıcaklığını artıran ısı enerjisine dönüştürülür, yani yüzey ısıtmasını gerçekleştirir. Akım frekansı ne kadar yüksek olursa, yüzey ve iş parçasının iç kısmı arasındaki akım yoğunluğu farkı o kadar büyük ve ısıtma tabakası o kadar incedir. Isıtma tabakasının sıcaklığı, çeliğin kritik nokta sıcaklığını aştığında, yüzeyde su vermenin sağlanması için hızla soğutulur. İndüksiyonla ısıtma prensibinden, akımın penetrasyon derinliğinin, indüksiyon bobini boyunca akımın frekansı ayarlanarak uygun şekilde değiştirilebileceği bilinebilir. Ayarlanabilir derinlik aynı zamanda indüksiyonlu ısıl işlemin önemli bir avantajıdır. Bununla birlikte, indüksiyonla sertleştirme teknolojisi, zayıf uyarlanabilirliği nedeniyle karmaşık mekanik iş parçaları için uygun değildir. Söndürülen iş parçasının yüzey tabakası daha büyük bir sıkıştırma iç gerilimine sahip olmasına rağmen, yorulma kırılma direnci daha yüksektir. Ancak sadece basit iş parçalarının montaj hattı üretimi için uygundur.
Şu anda, indüksiyonla sertleştirme teknolojisinin uygulanması esas olarak krank yüzeyinin su vermesinde kullanılmaktadır.şafts ve kameraşaftotomotiv endüstrisinde s. Bu parçalar basit bir yapıya sahip olmasına rağmen çalışma ortamı sert olmakla birlikte, belirli bir derecede aşınma direncine, eğilme direncine ve parçaların performansına karşı dirence sahiptirler. Yorulma gereksinimleri, aşınma direncini ve yorulma direncini artırmak için indüksiyonla sertleştirme yoluyla performans gereksinimlerinin karşılanması için de en makul yöntemdir. içinde yaygın olarak kullanılmaktadır. yüzey işleme otomotiv endüstrisindeki bazı parçaların
2. Vakumlu indüksiyon eritme ekipmanı
Vakumlu indüksiyon ergitme ekipmanı, mekanik yapının eşleştirilmesi yoluyla fiili kullanımdaki prensibi gerçekleştirmek için indüksiyon ergitme teknolojisini kullanır. Ekipman genellikle endüksiyon bobinini ve malzemeyi kapalı bir boşluğa koymak ve kaptaki gazı bir vakum pompalama sistemi ile çıkarmak için elektromanyetik indüksiyon prensibini kullanır ve ardından akımı endüksiyon bobininden geçirmek için güç kaynağını kullanır. indüklenmiş bir elektromotor kuvveti oluşturur ve malzemenin içinde olur Bir girdap oluşur ve ısı üretimi belirli bir seviyeye ulaştığında malzeme erimeye başlar. Eritme işlemi sırasında, ekipman üzerindeki diğer destekleyici bileşenler aracılığıyla güç kontrolü, sıcaklık ölçümü, vakum ölçümü ve ek besleme gibi bir dizi işlem gerçekleştirilir ve son olarak sıvı metal, pota ters çevrilmesi yoluyla kalıba dökülür. metal külçe. Koku. Vakum indüksiyon eritme ekipmanının ana yapısı aşağıdaki parçaları içerir:
Yukarıdaki bileşenlere ek olarak, vakumlu ergitme fırını, ekipmana malzemeyi eritmek için enerji girişi sağlamak ve kilit parçalarda belirli bir miktarda soğutma sağlamak için bir güç kaynağı, bir kontrol sistemi ve bir soğutma sistemi ile de donatılmalıdır. sistemin aşırı ısınmasını ve yapısal ömrün azalmasına veya hasara neden olmasını önlemek için. Spesifik proses gereksinimleri olan indüksiyon eritme ekipmanı için, transmisyon arabası, fırın kapısı açma ve kapama, santrifüj döküm tavası, gözlem penceresi vb. gibi ilgili yardımcı bileşenler vardır. Daha fazla kirlilik içeren ekipman için ayrıca bir gaz filtresi ile donatılmalıdır. sistem vb. Gerekli bileşenlere ek olarak, eksiksiz bir indüksiyon eritme ekipmanı setinin, belirli işlem gereksinimlerine göre diğer bileşenleri ekleyerek farklı işlevleri gerçekleştirebileceği ve metal hazırlama için uygun koşullar ve uygulama yöntemleri sağladığı görülebilir.
2.1. Vakum indüksiyon eritme fırını
Vakum indüksiyonlu ergitme fırını, önce vakum altında indüksiyonla ısıtma ile metali eriten ve daha sonra bir metal külçe elde etmek için sıvı metali bir kalıba döken bir eritme ekipmanıdır. Vakum indüksiyon fırınlarının gelişimi 1920 civarında başladı ve esas olarak nikel-krom alaşımlarını eritmek için kullanıldı. İkinci Dünya Savaşı, vakum teknolojisinin ilerlemesini teşvik edene kadar, vakumlu indüksiyon eritme fırını gerçekten geliştirildi. Bu dönemde, alaşımlı malzemelere olan talep nedeniyle, vakumlu indüksiyon eritme fırınları, ilk birkaç tonluktan düzinelerce tonluk ultra büyük endüksiyon fırınına kadar büyük ölçekli olarak gelişmeye devam etti. Seri üretime uyum sağlamak için, ekipman kapasitesindeki değişime ek olarak, indüksiyon ocağının yapısı da ünite olarak çevrimli bir çevrimli fırından, şarj, kalıp için sürekli veya yarı sürekli vakumlu indüksiyon eritme yöntemine dönüşmüştür. hazırlama, eritme ve dökme işlemleri. Fırını durdurmadan sürekli çalışma, şarj süresinden ve külçenin soğuması için bekleme süresinden tasarruf sağlar. Sürekli üretim verimliliği arttırır ve ayrıca alaşım çıkışını da arttırır. Gerçek üretimin ihtiyaçlarını daha iyi karşılayın. Yabancı ülkelerle karşılaştırıldığında, ülkemdeki erken vakumlu endüksiyon fırınları, esas olarak 2 tonun altında olmak üzere nispeten küçük kapasiteye sahiptir. Büyük ölçekli ergitme fırınları hala yurt dışından yapılan ithalata bel bağlamaktadır. Son on yılların gelişmesiyle, ülkem de kendi başına büyük ölçekli vakumlu indüksiyon eritme geliştirebilir. Fırın, maksimum eritme on tondan fazla ulaşır. VIM vakumlu indüksiyon eritme fırını daha önce geliştirilmiş, basit yapısı, rahat kullanımı ve düşük bakım maliyeti ile gerçek üretimde yaygın olarak kullanılmaktadır.
Vakum indüksiyon eritme fırınının temel şekli. Metal malzemeler, döner bir taret aracılığıyla eritme potasına eklenir. Diğer taraf pota ile hizalanır ve sıcaklık ölçümü, termokuplun erimiş metalin içine sokulmasıyla gerçekleştirilir. Eritilmiş metal, döndürme mekanizması tarafından tahrik edilir ve metalin eritilmesini gerçekleştirmek için şekillendirme kalıbına dökülür. Tüm süreç basit ve kullanımı kolaydır. Her eritme işleminin tamamlanması için bir veya iki işçi gerekir. Eritme işlemi sırasında, gerçek zamanlı sıcaklık izleme ve malzeme bileşiminin ayarlanması sağlanabilir ve nihai metal malzeme, işlem gereksinimleriyle daha uyumludur.
2.2. Vakum indüksiyon membran gaz ocağı
Bazı malzemeler için proseste dökümün vakum odasında tamamlanması gerekmez, sadece vakum ortamında ısının korunması ve gazdan arındırılması gerekir. VIM fırını temelinde, VID gazdan arındırma fırınının vakumlu indüksiyon membranlı gaz fırını yavaş yavaş geliştirilmektedir.
Vakum indüksiyonlu gaz giderme fırınının ana özelliği, kompakt yapı ve küçük fırın hacmidir. Daha küçük bir hacim, hızlı gaz ekstraksiyonu ve daha iyi bir vakum için daha elverişlidir. Geleneksel gaz giderme fırınları ile karşılaştırıldığında, ekipman nispeten küçük hacimli, düşük sıcaklık kaybı, daha iyi esneklik ve ekonomiye sahiptir ve sıvı veya katı besleme için uygundur. VID fırını, özel çelik ve demir dışı metallerin eritilmesi ve gazdan arındırılması için kullanılabilir ve atmosferik bir ortam veya koruyucu bir atmosfer koşullarında kalıba dökülmesi gerekir. Tüm eritme işlemi, işlem gereksinimlerini karşılamak için kimyasal bileşimin hassas bir şekilde ayarlanmasına elverişli olan dekarburizasyon ve malzemelerin rafine edilmesi, dehidrojenasyon, deoksidasyon ve kükürt giderme gibi safsızlıkların giderilmesini gerçekleştirebilir.
Belirli bir vakum koşulu veya koruyucu atmosfer altında, metal malzeme, indüksiyon gaz giderme fırınının ısıtılmasıyla kademeli olarak eritilir ve bu işlemde dahili gaz çıkarılabilir. İşlemde uygun bir reaksiyon gazı eklenirse, fırından çıkarılacak gaz halindeki karbürleri oluşturmak için metal içindeki karbon elementi ile birleşecek ve dekarbürizasyon ve rafinasyon amacına ulaşacaktır. Dökme işleminde, gazı alınmış metal malzemenin atmosferdeki gazdan izole edilmesini sağlamak için belirli bir koruyucu atmosferin getirilmesi gerekir ve son olarak metal malzemenin gazdan arındırılması ve rafine edilmesi tamamlanır.
2.3. Vakum indüksiyon gaz giderme döküm fırını
Vakum indüksiyonlu gaz giderme döküm fırını, ilk iki eritme teknolojisi temelinde geliştirilmiştir. 1988 yılında, Alman ALD şirketinin öncülü olan Leybold-Heraeus, ilk VIDP fırınını üretti. Bu fırın tipinin teknik çekirdeği, indüksiyon bobini potasıyla entegre edilmiş kompakt bir vakumlu eritme odasıdır. İndüksiyon bobininden sadece biraz daha büyüktür ve sadece indüksiyon bobini ve potayı içerir. Kablolar, su soğutma boru hatları ve hidrolik devir mekanizması, eritme odasının dışına kurulur. Avantajı, kabloları ve su soğutmalı boru hatlarını erimiş çeliğin sıçramasından ve sıcaklık ve basınçtaki periyodik değişikliklerden kaynaklanan hasarlardan korumaktır. Sökme kolaylığı ve potanın değiştirilmesini kolaylaştırması nedeniyle VIDP fırın kabuğu, üç fırın gövdesi ile donatılmıştır. Hazırlık potalı fırın astarı, üretim döngüsünü kısaltır ve üretim verimliliğini artırır.
Fırın kapağı, fırın çerçevesi ve iki hidrolik silindir kolonu üzerinde vakumla kapatılmış olarak desteklenir. yataks. Dökme sırasında, iki hidrolik silindir fırın kapağını yanda üst üste getirir ve fırın kapağı, eritme odasını vakum etrafında eğilmesi için çalıştırır. yatak. Eğimli dökme durumunda, eritme odası ile indüksiyon bobini potası arasında nispi bir hareket yoktur. Yolluk, VIDP fırınının önemli bir parçasıdır. VIDP fırınının tasarımı, eritme odasını külçe odasından izole ettiğinden, erimiş çelik, vakumlu kanaldan külçe odasına geçmelidir. Külçe odası, kare bir eğik kenar ile açık ve kapalıdır. İki bölümden oluşmaktadır. Sabit kısım, yolluk haznesine bitişiktir ve hareketli kısım, külçe haznesinin açılıp kapanmasını tamamlamak için zemin yolu boyunca yatay olarak hareket eder. Bazı ekipmanlarda hareketli kısım 30 derece, sağa ve sola açık olacak şekilde tasarlanmıştır, bu da külçe kalıpların yüklenmesi ve boşaltılması ve vinçlerin günlük bakım ve onarımı için uygundur. Ergitme başlangıcında fırın gövdesi alttaki hidrolik mekanizma ile kaldırılır, fırının üst yapısı fırın kapağı ile birleştirilir ve özel bir mekanizma ile kilitlenir. Fırın kapağının üst ucu, bir vakum vasıtasıyla besleme odasına bağlanır. valf.
Sadece eritme kısmı vakum odasına kapatıldığından ve saptırma oluğundan dışarı döküldüğünden, fırın yapısı kompakttır, eritme odası daha küçüktür ve vakum daha iyi ve daha hızlı kontrol edilebilir. Geleneksel indüksiyon eritme fırını ile karşılaştırıldığında, kısa tahliye süresi ve düşük sızıntı oranı özelliklerine sahiptir. İdeal basınç kontrolü, PLC mantık kontrol sistemi donatılarak elde edilebilir. Aynı zamanda, elektromanyetik karıştırma sistemi erimiş havuzu istikrarlı bir şekilde karıştırabilir ve eklenen elementler, sıcaklığı sabit tutarak erimiş havuzda yukarıdan aşağıya düzgün bir şekilde çözülür. Para dökerken, döküm deliğinin ilk döküm tıkanıklığını ve yolluk termal çatlamasını azaltmak için yolluk harici ısıtma sistemi tarafından ısıtılır. Filtre bölmesi ve diğer önlemleri ekleyerek erimiş çeliğin etkisini azaltabilir ve metal saflığını iyileştirebilir. VIDP fırınının küçük hacmi nedeniyle vakum kaçağı tespiti ve onarımı daha kolaydır ve fırında temizleme süresi daha kısadır. Ek olarak, fırındaki sıcaklık küçük, değiştirilmesi kolay bir termokupl ile ölçülebilir.
2.4, indüksiyon su soğutmalı pota
Su soğutmalı pota elektromanyetik indüksiyon vakumlu levitasyonlu ergitme yöntemi, son yıllarda hızla gelişen bir ergitme yöntemidir. Esas olarak yüksek erime noktalı, yüksek saflıkta ve son derece aktif metal veya metal olmayan malzemeler hazırlamak için kullanılır. Bakır potayı bakır petal yapısının eşit parçalarına keserek ve her petal bloktan su soğutması geçirilerek, bu yapı elektromanyetik itmeyi arttırır, böylece erimiş metal ortada sıkıştırılarak bir kambur oluşturur ve ondan kopar. pota duvarı. Metal, alternatif bir elektromanyetik alana yerleştirilir. Cihaz, pota içindeki hacim boşluğundaki kapasiteyi yoğunlaştırır ve ardından yükün yüzeyinde güçlü bir girdap akımı oluşturur. Bir yandan yükü eritmek için Joule ısısı yayar, diğer yandan eritmek için Lorentz kuvveti oluşturur. Eklenen alaşım elementleri, eriyik içinde hızlı ve eşit bir şekilde karıştırılabilir, bu da kimyasal bileşimi daha düzgün ve sıcaklık iletimini daha dengeli hale getirir. Manyetik levitasyonun etkisinden dolayı, eriyik potanın iç duvarı ile temas etmez, bu da potanın eriyiği kirletmesini önler. Aynı zamanda, ısı iletimini azaltır ve erimiş metalin ısı yayılımını azaltan ve daha yüksek bir sıcaklığa ulaşan ısı radyasyonunu arttırır. Eklenen metal şarjı için gerekli süreye ve ayarlanan sıcaklığa göre eritilip sıcak tutulabilir ve şarjın önceden işlenmesine gerek yoktur. Su soğutmalı pota eritme, buharlaşma kaybı daha küçükken ve enerji tüketimi daha düşükken ve üretim verimliliği artarken, metal inklüzyonlarının giderilmesi ve gazdan arındırma rafinerisi açısından elektron ışını eritme seviyesine ulaşabilir. İndüksiyonla ısıtmanın temassız ısıtma özelliklerinden dolayı, eriyik üzerindeki etki daha küçüktür ve daha yüksek saflıkta veya aşırı aktif metallerin hazırlanmasında iyi bir etkiye sahiptir. Ekipmanın karmaşık yapısı nedeniyle, büyük kapasiteli ekipman için maglev eritme işlemini gerçekleştirmek hala zordur. Bu aşamada büyük kapasiteli su soğutmalı bakır pota ergitme ekipmanı bulunmamaktadır. Mevcut su soğutmalı pota ekipmanı, yalnızca küçük hacimli metal eritme üzerine deneysel araştırmalar için kullanılmaktadır.
3. İndüksiyon eritme ekipmanının gelecekteki gelişim eğilimi
Vakum indüksiyonlu ısıtma teknolojisinin gelişmesiyle birlikte, farklı işlevler elde etmek için fırın tipleri sürekli değişmektedir. Basit bir eritme veya ısıtma yapısından, yavaş yavaş farklı işlevleri gerçekleştirebilen ve üretime daha elverişli karmaşık bir yapıya dönüşmüştür. Gelecekteki daha karmaşık teknolojik süreçler için, hassas süreç kontrolünün nasıl sağlanacağı, ilgili bilgilerin nasıl ölçüleceği ve çıkarılacağı ve işçilik maliyetlerinin mümkün olduğunca nasıl azaltılacağı, indüksiyon eritme ekipmanının geliştirme yönüdür.
3.1, modüler
Eksiksiz bir ekipman setinde, farklı kullanım gereksinimleri için farklı bileşenler donatılmıştır. Bileşenin her bir parçası, kendi kullanım amacına ulaşmak için kendi işlevini yerine getirir. Belirli fırın türleri için, ekipmanı daha eksiksiz hale getirmek için belirli modüllerin eklenmesi, örneğin eksiksiz bir sıcaklık ölçüm sistemi ile donatılmış olması, fırın içindeki malzemelerin sıcaklıkla değişimlerini gözlemlemeye ve sıcaklığın daha makul bir kontrolünü sağlamaya yardımcı olur; malzeme bileşimini tespit etmek için bir kütle spektrometresi ile donatılmış İşlemin geliştirme aşamasında alaşımın performansını iyileştirmek için alaşım elementleri ekleme zamanını ve sırasını ayarlayın; bazı refrakter metallerin erime problemini çözmek için bir elektron tabancası ve iyon tabancası ile donatılmıştır, vb. Gelecekteki endüksiyon metalurji ekipmanlarında, farklı işlevler elde etmek ve farklı süreç gereksinimlerini karşılamak için farklı modüllerin farklı kombinasyonları kaçınılmaz bir gelişme eğilimi haline geldi ve aynı zamanda farklı alanların bir kombinasyonu ve referansı oldu. Metal eritme sürecini iyileştirmek ve daha iyi performansa sahip malzemeler elde etmek için modüler ekipman daha güçlü pazar rekabet gücüne sahip olacaktır.
3.2. Akıllı kontrol
Geleneksel eritme ile karşılaştırıldığında, vakum indüksiyon ekipmanı, proses kontrolünü gerçekleştirmede büyük bir avantaja sahiptir. Bilgisayar teknolojisinin gelişmesi, insan-makine arayüzünün dostça çalışması, ekipmandaki akıllı sinyal alımı ve makul program ayarı nedeniyle, eritme sürecini kontrol etme amacına kolayca ulaşabilir, işçilik maliyetlerini azaltabilir ve işlemi daha basit hale getirebilir. uygun.
Gelecekteki geliştirmede, vakum ekipmanına daha akıllı kontrol sistemleri eklenecektir. Kurulan süreç için, insanların akıllı kontrol sistemi aracılığıyla eritme sıcaklığını hassas bir şekilde kontrol etmesi, belirli bir zamanda alaşım malzemeleri eklemesi ve bir dizi eritme, ısı koruma ve dökme işlemini tamamlaması daha kolay olacaktır. Ve tüm bunlar bilgisayar tarafından kontrol edilip kaydedilecek ve insan hatalarından kaynaklanan gereksiz kayıplar azaltılacaktır. Tekrarlayan eritme işlemi için daha uygun ve akıllı modern kontrol gerçekleştirebilir.
3.3. bilişim
İndüksiyon eritme ekipmanı, tüm eritme işlemi sırasında büyük miktarda eritme bilgisi üretecektir, indüksiyonlu ısıtma güç kaynağının gerçek zamanlı parametre değişiklikleri, şarjın sıcaklık alanı, pota, indüksiyon bobini tarafından üretilen elektromanyetik alan, metal eriyiğinin fiziksel özellikleri vb. Şu anda, ekipman yalnızca basit veri toplama gerçekleştirir ve analiz işlemi, eritme tamamlandıktan sonra veriler çıkarıldıktan sonra gerçekleştirilir. Gelecekte, bilişim, veri toplama ve işlemenin gelişimi ve analiz süreci kaçınılmaz olarak izabe süreci ile neredeyse senkronize olacaktır. Metalurjik ekipmanın dahili olarak eritilmiş malzemeleri için eksiksiz veri toplama, verilerin bilgisayarla işlenmesi, mevcut durumda ekipmanın dahili sıcaklık alanının ve elektromanyetik alanının gerçek zamanlı gösterimi ve farklı verilerin gerçek zamanlı geri bildirimi yoluyla sinyal iletimi, insanlar için uygun Eritme sürecinin gerçek zamanlı gözlemi ve ayarlanması, insan müdahalesini ve kontrolünü güçlendirdi. Eritme işleminde, işlemi iyileştirmek ve alaşım performansını iyileştirmek için zamanında ayarlamalar yapılır.
4 Sonuç
Endüstrinin ilerlemesiyle birlikte, vakumlu indüksiyon eritme teknolojisi, benzersiz avantajları ile son yıllarda muazzam bir şekilde gelişmiştir ve endüstriyel alanda önemli bir rol oynamaktadır. Şu anda, ülkemin vakumlu indüksiyonlu ergitme teknolojisi hala yabancı ülkelerin gerisinde kalsa da, ülkemin özel ergitme ekipmanının pazar rekabet gücünü artırmak ve dünyanın birinci sınıf ergitme ekipmanı olmak için elinden gelenin en iyisini yapmak için ilgili uygulayıcıların aralıksız çabalarını gerektiriyor. . Ön planda.
Bu makaleye bağlantı: Vakum indüksiyon eritme teknolojisinin gelişimi ve trendi
Yeniden Baskı Bildirimi: Özel bir talimat yoksa, bu sitedeki tüm makaleler orijinaldir. Lütfen yeniden basılacak kaynağı belirtin:https://www.cncmachingptj.com
PTJ®, eksiksiz bir bakır çubuk yelpazesi sağlayan özelleştirilmiş bir üreticidir. pirinç parçalar ve bakır parçalar. Yaygın üretim süreçleri arasında kesme, kabartma, bakırcılık, tel erozyon hizmetleri, dağlama, şekillendirme ve bükme, üzücü, sıcak dövme ve presleme, delme ve delme, diş açma ve tırtıl açma, kesme, çok milli işleme, ekstrüzyon ve metal dövme ve presleme. Uygulamalar arasında baralar, elektrik iletkenleri, koaksiyel kablolar, dalga kılavuzları, transistör bileşenleri, mikrodalga tüpleri, boş kalıp tüpleri ve toz metalurjisi ekstrüzyon tankları.
Bize projenizin bütçesi ve tahmini teslim süresi hakkında biraz bilgi verin. Hedefinize ulaşmanıza yardımcı olacak en uygun maliyetli hizmetleri sağlamak için sizinle birlikte strateji oluşturacağız, Doğrudan bizimle iletişime geçebilirsiniz ( satış@pintejin.com ).
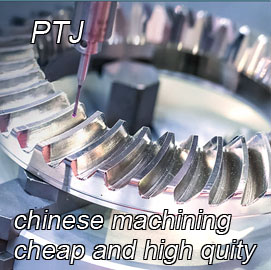
- 5 Eksen İşleme
- Cnc Frezeleme
- Cnc Tornalama
- İşleme Endüstrileri
- Işleme süreci
- Yüzey İşlem
- Metal İşleme
- Plastik İşleme
- Toz Metalurji Kalıbı
- Döküm Döküm
- Parça Galerisi
- Oto Metal Parçaları
- Makine parçaları
- LED Soğutucu
- Yapı Parçaları
- Mobil Parçalar
- Tıbbi Parçalar
- Elektronik parçalar
- Özel İşleme
- Bisiklet Parçaları
- Alüminyum İşleme
- titanyum işleme
- Paslanmaz Çelik İşleme
- Bakır İşleme
- Pirinç İşleme
- Süper Alaşımlı İşleme
- Peek İşleme
- UHMW İşleme
- Unilate İşleme
- PA6 İşleme
- PPS İşleme
- Teflon İşleme
- İnkonel İşleme
- Takım Çeliği İşleme
- Daha Fazla Malzeme