Yüksek Hassasiyetli Parçalar Nasıl İşlenir?
2023-09-22
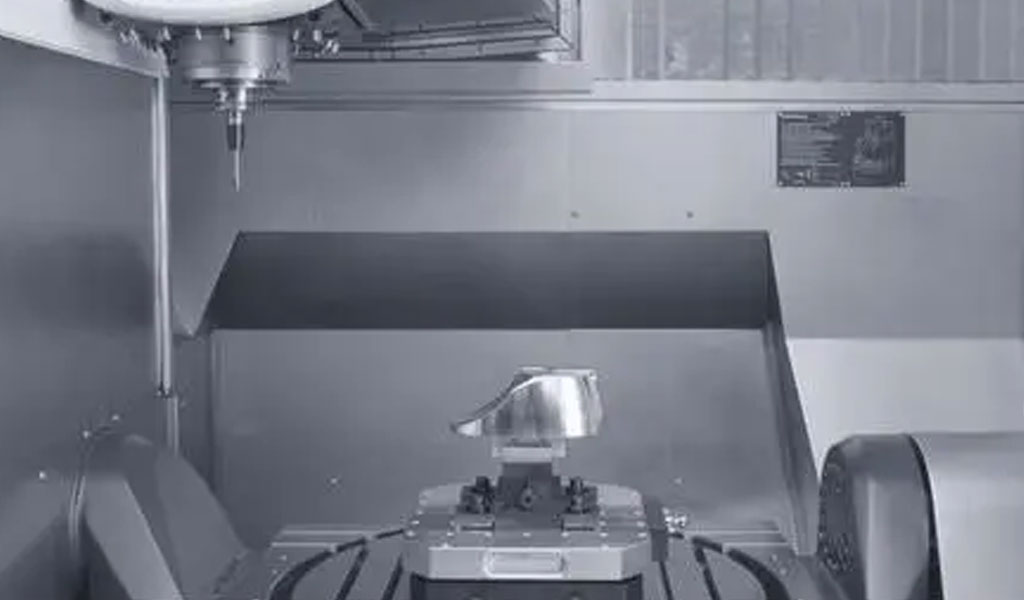
Hassas İşlemeyi Anlamak
Hassas işleme, çok çeşitli endüstrilerde kullanılan karmaşık ve doğru bileşenlerin üretiminden sorumlu olan modern imalatın temel taşıdır. Önemini tam olarak kavramak için, hassas işlemenin temel kavramlarını, çeşitli sektörlerdeki hayati rolünü ve mevcut mükemmellik durumuna ulaşan tarihsel yolculuğu inceleyelim.A. Hassas İşleme Nedir?
Hassas işleme, bir iş parçasından malzemeyi yüksek derecede doğruluk ve kontrolle kaldıran ve dar toleranslara sahip ince işlenmiş bileşenlerle sonuçlanan bir dizi üretim sürecini ifade eder. Bu işlem, metal, plastik veya seramik gibi ham maddeleri, kesin spesifikasyonları karşılayan hassas parçalara dönüştürür. Hassas işlemenin temel özellikleri şunları içerir:- doğruluk: Hassas işleme, nihai ürünün minimum sapmayla tam olarak amaçlanan tasarıma uymasını sağlar.
- Sıkı Toleranslar: Son derece sıkı toleranslara sahip parçaların üretilmesine olanak tanır, bu da bitmiş bileşenlerin belirtilen ölçümlere sıkı sıkıya bağlı olduğu anlamına gelir.
- Üstün Yüzey Cilası: Hassas işleme, olağanüstü yüzey kalitesi sağlar ve çoğu zaman ek son işlem işlemlerine olan ihtiyacı ortadan kaldırır.
- Karmaşık Geometriler: Karmaşık şekiller, konturlar ve özellikler oluşturabilmesi, karmaşık tasarımlara sahip bileşenlerin üretiminde onu vazgeçilmez kılmaktadır.
- Tekrarlanabilirlik: Kesinlik Işleme süreciYüksek düzeyde tekrarlanabilirlik sayesinde birden fazla parçada tutarlı kalite sağlanır.
- Çok yönlülük: Çok çeşitli malzemelere uygulanabilmesi, onu çeşitli endüstrilere uygun hale getirir.
B. Hassas İşlemenin Önemi
Hassas işleme, birçok kritik endüstride büyük önem taşıyor ve günlük hayatımızın çeşitli yönlerini etkiliyor. İşte öneminin bazı zorlayıcı nedenleri:- Havacılık ve Uzay Sanayi: Havacılık ve uzay sektöründe zorlu koşullara dayanabilen bileşenlerin işlenmesi için hassas işleme vazgeçilmezdir. Uçak motorları, iniş dişlive yapısal elemanlar güvenlik ve performans açısından hassas işlenmiş parçalara dayanır.
- Tıbbi Cihazlar: Cerrahi aletler, protezler ve implante edilebilir cihazlar gibi tıbbi cihazlar biyouyumluluk, doğruluk ve hasta güvenliği açısından hassas işleme gerektirir.
- Otomotiv sektörü: Hassas işlenmiş parçalar, otomotiv endüstrisinin araçların güvenilirliğini ve verimliliğini sağlaması açısından önemlidir. Motor parçaları, şanzıman sistemleri ve fren mekanizmaları gibi bileşenler hassas işlemeye dayanır.
- Elektronik ve Yarı İletkenler: Hassas işleme, işlevsellik için çok küçük toleransların zorunlu olduğu mikroelektronik bileşenlerin ve yarı iletken cihazların üretiminde çok önemlidir.
- Enerji sektörü: Enerji endüstrisi, türbinler, jeneratörler ve iletim bileşenleri dahil olmak üzere enerji üretiminde kullanılan kritik parçaların üretimi için hassas işlemeye güvenmektedir.
- Takım ve Kalıp Yapımı: Hassas işleme, takımların ve kalıpların imalatında çok önemlidir ve bunlar da sayısız başka ürün yaratmak için kullanılır.
- Tüketici Elektroniği: Akıllı telefonların, dizüstü bilgisayarların ve diğer tüketici elektroniklerinin üretiminde, şık tasarımlar ve optimum işlevsellik sağlamak için hassas işlemeden yararlanılır.
- Araştırma ve Geliştirme: Araştırmacılar ve bilim adamları deneyler, prototipler ve laboratuvar ekipmanları için hassas işlenmiş bileşenlere güveniyorlar.
C. Tarihsel Perspektif
Hassas işleme yolculuğunun izleri, yetenekli zanaatkarların malzemeleri şekillendirmek için ilkel aletler kullandığı eski uygarlıklara kadar uzanır. Ancak o dönemde elde edilen hassasiyet günümüz standartlarına göre sınırlıydı.- Erken Hassas İşleme: 18. ve 19. yüzyıllardaki sanayi devrimi, hassas işlemenin geliştirilmesinde çok önemli bir döneme işaret ediyordu. Torna ve freze makineleri gibi takım tezgahlarının icadı, daha fazla doğruluk ve tutarlılık sağlayarak imalatta devrim yarattı.
- Dünya Savaşı II: Hassas işleme, askeri teçhizatın gerekli hassasiyet ve tekdüzelik ile üretilmesi için gerekli olduğundan, II. Dünya Savaşı'nda çok önemli bir rol oynadı. Bu çağ, işleme tekniklerindeki ilerlemelere ve yeni malzemelerin ortaya çıkışına tanık oldu.
- Savaş Sonrası Gelişmeler: Savaş sonrası dönemde bilgisayarlı sayısal kontrol (CNC) makinelerinin kullanımı da dahil olmak üzere teknolojik yeniliklerde bir artış yaşandı. CNC'de işleme Otomatik ve son derece hassas operasyonlara izin vererek yeni bir üretim çağını başlattı.
- Dijital Çağ: Bilgisayarların ve yazılımın işleme süreçlerine entegrasyonu hassas işlemeyi daha da artırdı. Modern CNC makineleri, karmaşık işlemleri benzersiz bir doğrulukla yürütebiliyor ve bu da onları günümüzün üretim ortamında vazgeçilmez kılıyor.
Malzemeler ve Önemi
Malzemeler hassas işlemenin temelidir ve doğru malzemenin seçimi yüksek hassasiyetli parçaların üretiminde çok önemli bir rol oynar. Bu bölümde uygun malzemeleri seçmenin önemine değineceğiz, malzeme özelliklerinin önemini anlayacağız ve işlenebilirliği etkileyen çeşitli faktörleri inceleyeceğiz.A. Malzemelerin Seçimi
Hassas işlemede malzeme seçimi, nihai ürünün performansını, dayanıklılığını ve işlevselliğini doğrudan etkileyen kritik bir karardır. Üreticiler malzeme seçerken çeşitli faktörleri göz önünde bulundurmalıdır:- Malzeme Uygunluğu: Malzeme amaçlanan uygulamaya uygun olmalıdır. Farklı endüstriler ve uygulamaların sıcaklık direnci, korozyon direnci ve elektrik iletkenliği gibi farklı gereksinimleri vardır.
- Mekanik özellikler: Çekme mukavemeti, sertlik ve süneklik gibi mekanik özellikler çok önemlidir. Örneğin havacılıkta yapısal bileşenler için çekme dayanımı yüksek malzemeler tercih edilmektedir.
- Termal Özellikler: Bazı uygulamalar mükemmel ısı iletkenliğine veya yüksek sıcaklıklara dayanıklı malzemelere ihtiyaç duyar. Bu özellikle enerji üretimi ve elektronik gibi endüstrilerde önemlidir.
- Korozyon Direnci: Korozyonun söz konusu olduğu ortamlarda paslanmaz çelik veya titanyum gibi korozyona karşı direnci yüksek malzemeler tercih edilir.
- Ağırlıkla İlgili Hususlar: Otomotiv ve havacılık gibi endüstriler, yakıt tüketimini azaltmak ve performansı artırmak için genellikle alüminyum veya karbon fiber kompozitler gibi hafif malzemelere öncelik verir.
- Maliyet Kısıtlamaları: Malzeme seçiminde maliyet önemli bir faktördür. Yüksek performanslı malzemeler pahalı olabilir, bu nedenle üreticilerin performans ile maliyet etkinliği arasında bir denge kurması gerekir.
- Yasal Uygunluk: Sağlık hizmetleri gibi endüstrilerde malzemelerin biyouyumluluk ve güvenlik açısından sıkı düzenleyici standartları karşılaması gerekir.
- Uygunluk: Malzemelerin mevcudiyeti ve kaynakları da seçimi etkiler. Bazı özel alaşımlar veya kompozitlerin bulunabilirliği sınırlı olabilir.
B. Malzeme Özellikleri
Hassas işleme için malzemelerin özelliklerini anlamak çok önemlidir. İşte bazı önemli malzeme özellikleri ve bunların önemi:- Gerilme direnci: Çekme mukavemeti, bir malzemenin çekme kuvvetine kırılmadan dayanma yeteneğini ölçer. Mekanik strese maruz kalan yapısal bileşenler ve parçalar için gereklidir.
- Sertlik: Sertlik, bir malzemenin deformasyona ve aşınmaya karşı direncini gösterir. Sert malzemeler kesici takımlar için uygundur, ancak contalar gibi belirli uygulamalar için daha yumuşak malzemeler tercih edilebilir.
- yumuşaklık: Süneklik, bir malzemenin çekme gerilimine maruz kaldığında kırılmadan deforme olma yeteneğini ifade eder. Sünek malzemelerin şekillendirilmesi daha kolaydır ancak sertlik gerektiren uygulamalar için uygun olmayabilir.
- Termal iletkenlik: Yüksek ısı iletkenliğine sahip malzemeler ısıyı verimli bir şekilde dağıtır. Bu özellik sıcaklık kontrolünün kritik olduğu uygulamalarda hayati öneme sahiptir.
- Elektiriksel iletkenlik: Malzemelerin elektrik akışını kolaylaştırması gereken elektronik ve elektrikli bileşenlerde elektriksel iletkenlik önemlidir.
- Manyetik özellikler: Manyetik özellikler, malzemelerin ferromanyetik veya manyetik olmayan olmasının gerekebileceği elektromanyetik ve elektronik gibi endüstrilerde önemlidir.
- Kimyasal direnç: Malzemeler asitlere, bazlara veya diğer aşındırıcı maddelere maruz kaldıkları ortamlarda kimyasal korozyona dayanıklı olmalıdır.
C. İşlenebilirlik Faktörleri
İşlenebilirlik, bir malzemenin işlenebilme, kesilebilme veya şekillendirilebilme kolaylığını ifade eder. Aşağıdakiler de dahil olmak üzere çeşitli faktörlerden etkilenir:- Malzeme Sertliği: Daha yumuşak malzemelerin işlenmesi genellikle daha kolaydır, daha sert malzemelerin işlenmesi ise özel alet ve teknikler gerektirebilir.
- Talaş Oluşumu: Talaşlı imalat sırasında talaş oluşumu ve tahliyesi prosesin verimliliğini ve yüzey kalitesini etkiler.
- Takım Aşınması: Farklı malzemeler, işleme hızını ve maliyetini etkileyen, değişen derecelerde takım aşınmasına neden olabilir.
- Soğutucu ve Yağlama: İşleme sırasında sürtünmeyi, ısıyı ve takım aşınmasını azaltmak için uygun soğutma sıvısı ve yağlama şarttır.
- kesme Hızı: Kesici takımın malzeme içerisinde hareket etme hızı hem verimliliği hem de işlenen yüzeyin kalitesini etkiler.
- Alet Malzemesi: Karbür veya yüksek hız çeliği gibi kesici takım malzemesinin seçimi, işlenen malzemeye bağlıdır.
- Kesme parametreleri: İlerleme hızı ve kesme derinliği gibi kesme parametrelerinin ayarlanması, belirli malzemeler için işleme sürecini optimize edebilir.
Hassas İşleme için Takım Tezgahları
Takım tezgahları, ham maddelerin yüksek hassasiyetli parçalara dönüştürülmesini sağlayan hassas işlemenin kalbidir. Bu bölümde hassas işlemede kullanılan dört temel takım tezgahı türünü inceleyeceğiz: CNC İşleme Merkezleri, Tornalama Tezgahları, Taşlama Tezgahları ve EDM (Elektrikli Deşarj İşleme). Bu makinelerin her biri hassas bileşenlerin üretiminde benzersiz bir rol oynamaktadır.A. CNC İşleme Merkezleri
CNC (Bilgisayarlı Sayısal Kontrol) işleme merkezleri çok yönlüdür ve hassas işlemede yaygın olarak kullanılır. Kesici takımların ve iş parçalarının hareketini olağanüstü hassasiyetle kontrol eden otomatik sistemlerdir. İşte CNC işleme merkezlerine ve bunların önemine genel bir bakış:- Çok yönlülük: CNC işleme merkezleri, frezeleme, delme ve kılavuz çekme dahil olmak üzere çeşitli işleme işlemlerini gerçekleştirebilir. Bu çok yönlülük, birden fazla özelliğe sahip karmaşık parçaların üretilmesine olanak tanır.
- Yüksek Hassasiyetli: CNC makinelerinin bilgisayarlı kontrolü, hassas takım konumlandırma ve tutarlı sonuçlar sağlar, bu da onları dar toleranslı parçalar için ideal kılar.
- Otomasyon: CNC işleme merkezleri minimum insan müdahalesiyle sürekli olarak çalışabilir. Bu otomasyon verimliliği artırır ve hata riskini azaltır.
- Karmaşık Geometriler: Karmaşık şekillerin ve konturların işlenmesinde üstündürler, bu da onları karmaşık bileşenlerin yaygın olduğu havacılık ve uzay gibi endüstriler için uygun hale getirir.
- Tekrarlanabilir Sonuçlar: CNC makineleri mükemmel tekrarlanabilirlik sunarak üretilen her parçanın tasarımın özelliklerine tam olarak uymasını sağlar.
- Daha Kısa Kurulum Süreleri: CNC işleme merkezleri, farklı görevler arasında hızla geçiş yapacak şekilde programlanabilir, böylece kurulum süreleri en aza indirilir ve üretim verimliliği artar.
B. Torna Makinaları
Tornalama makineleri, bir kesici takım malzemeyi dış yüzeyinden çıkarırken iş parçasını döndürerek silindirik parçalar oluşturmak için kullanılır. Üretmek için gereklidirler şaftdönme simetrisine sahip s, pimler ve diğer bileşenler. Tornalama makineleriyle ilgili önemli noktalar şunlardır:- Silindirik Parçalar: Tornalama makineleri, dişli veya karmaşık oluklu olanlar da dahil olmak üzere silindirik veya boru şeklinde bileşenlerin üretiminde uzmanlaşmıştır.
- Yüksek Hızlar: Yüksek hızlarda çalışırlar, bu da onları pürüzsüz ve hassas yüzey gerektiren parçalar için uygun kılar.
- Tek Eksenli Çalışma: Tornalama makinelerinin çoğu tek eksenlidir ve iş parçasının dış yüzeyinin şekillendirilmesine odaklanır.
- Seri Üretim için Verimli: Tornalama, minimum malzeme israfıyla seri üretim parçaları için oldukça verimlidir.
- Torna Makineleri: Manuel ve CNC kontrollü torna tezgahları yaygın olarak kullanılan, çeşitli yetenekler sunan torna tezgahlarıdır.
C. Taşlama Makinaları
Taşlama makineleri, sert veya aşındırıcı malzemelerin hassas yüzey işlemleri ve şekillendirilmesi için tasarlanmıştır. Son derece sıkı toleranslar ve üstün yüzey kalitesi elde etmek için çok önemlidirler. Taşlama makinelerinin neden önemli olduğu aşağıda açıklanmıştır:- Mikron Düzeyinde Hassasiyet: Taşlama makineleri mikron düzeyinde hassasiyete ulaşabiliyor, bu da onları en yüksek düzeyde doğruluk gerektiren uygulamalar için vazgeçilmez kılıyor.
- Malzeme Kaldırma: Malzemeyi aşındırarak çıkarır, yüzey kusurlarının düzeltilmesine ve olağanüstü pürüzsüzlük elde edilmesine olanak tanır.
- Takım ve Kesici Taşlama: Yüzey taşlamanın yanı sıra kesici takımların bilenmesi ve hassas profillerin üretilmesi için özel taşlama makinaları bulunmaktadır.
- Çeşitli Taşlama Yöntemleri: Yüzey taşlama makineleri, silindirik taşlama makineleri ve puntasız taşlama makineleri dahil olmak üzere farklı taşlama makineleri türleri, çeşitli işleme ihtiyaçlarını karşılar.
- Sertleştirilmiş Malzemeler: Taşlama, geleneksel işleme yöntemlerinin etkisiz olabileceği takım çeliği ve seramik gibi sertleştirilmiş malzemeler için özellikle uygundur.
D. EDM (Elektrik Deşarjı İşleme)
EDM veya Elektrik Erozyon İşleme, malzemeleri şekillendirmek için elektrik deşarjlarını kullanan geleneksel olmayan bir işleme işlemidir. Geleneksel kesme aletlerinin hasara neden olabileceği karmaşık ve hassas parçalar oluşturmak için idealdir. EDM'nin temel yönleri şunları içerir:- Fiziksel Temas Yok: EDM, takım ile iş parçası arasında doğrudan fiziksel temas gerektirmez, bu da takımın aşınması ve kırılgan malzemelerin hasar görmesi riskini en aza indirir.
- Yüksek Hassasiyetli: Olağanüstü sert malzemelerde bile yüksek hassasiyet ve yüzey kalitesi elde edilebilir.
- Tel Erozyon ve Sinker Erozyon: EDM makinelerinin iki ana türü vardır: Tel kesme Bir tel elektrot kullanan EDM ve şekillendirilmiş bir elektrot kullanan platin EDM.
- Karmaşık Şekiller: EDM, karmaşık ayrıntılara ve ince özelliklere sahip kalıplar ve kalıplar gibi karmaşık şekiller üretebilir.
- Sıcaktan etkilenmiş alan: EDM iş parçasında ısı üretmediğinden havacılık alaşımları gibi ısıya duyarlı malzemeler için uygundur.
- Yavaş Süreç: EDM, diğer işleme yöntemleriyle karşılaştırıldığında nispeten yavaştır; bu da onu düşük adetli, yüksek hassasiyetli işler için en uygun hale getirir.
Kesici Takımlar ve Takımlar
Hammaddeleri şekillendiren ve yüksek hassasiyetli parçalara dönüştüren aletler olarak hizmet veren kesici takımlar, hassas işlemenin ön saflarında yer alır. Bu bölümde çeşitli kesici takım türlerini, takım kaplamalarının önemini ve takım ömrü ile aşınmayı etkileyen faktörleri inceleyeceğiz.A. Kesici Takım Çeşitleri
Hassas işleme, her biri belirli görevler ve malzemeler için tasarlanmış çok çeşitli kesici takımlara dayanır. Kesici takım seçimi, işleme sürecinin verimliliğini ve doğruluğunu büyük ölçüde etkiler. İşte bazı yaygın kesici takım türleri:- Frezeler: Parmak frezeler, frezeleme operasyonlarında kullanılan çok yönlü takımlardır. Birden fazla kesme kenarına sahiptirler ve yüzey işleme, konturlama ve kanal açma dahil olmak üzere çeşitli yollarla malzemeyi iş parçasından kaldırabilirler.
- Matkaplar: Matkaplar iş parçalarında delik açmak için tasarlanmıştır. Burgulu matkaplar, merkezi matkaplar ve değiştirilebilir matkaplar dahil olmak üzere çeşitli biçimlerde gelirler.
- Torna Uçları: Torna tezgahlarında silindirik parçalara şekil vermek amacıyla kullanılırlar. Tornalama uçları, farklı uygulamalara uyacak şekilde çeşitli şekil ve malzemelerde mevcuttur.
- Freze Bıçakları: Freze takımları yüzey frezeleri, bilyalı değirmenler ve kanal açma takımları gibi farklı şekillerde gelir ve freze makinelerinde iş parçası üzerinde çeşitli özellikler oluşturmak için kullanılır.
- Raybaları: Raybalar, önceden açılmış deliklerin hassas boyutlara getirilmesi ve boyutlandırılması için kullanılır. Pürüzsüz ve doğru delik yüzeyleri sağlarlar.
- Kılavuzlar ve Kalıplar: Bu kesici takımlar diş açma işlemlerinde kullanılır. Kılavuzlar iç dişler oluştururken, kalıplar dış dişler oluşturur.
- Taşlama: Taşlama taşları hassas yüzey taşlamada kullanılan aşındırıcı aletlerdir. Çeşitli aşındırıcı malzemelerde ve tane boyutlarında mevcutturlar.
- Broşlar: Broşlar, kama yuvaları ve kamalar gibi iç ve dış şekilleri ve profilleri kesmek için kullanılan özel aletlerdir.
- Havşalar ve Havşalar: Bu aletler, deliklerin etrafında girintiler veya pahlar oluşturmak için kullanılır. raptiyes.
- Sıkıcı Barlar: Delik baraları, delik işleme operasyonlarında mevcut deliklerin hassas bir şekilde büyütülmesi amacıyla kullanılır.
B. Takım Kaplamaları
Takım kaplamaları, kesici takımların performansını ve dayanıklılığını artırmak için onlara uygulanan ince malzeme katmanlarıdır. Bu kaplamalar çeşitli avantajlar sunar:- Azaltılmış Sürtünme: Titanyum nitrür (TiN) ve titanyum karbonitrür (TiCN) gibi kaplamalar, takım ile iş parçası arasındaki sürtünmeyi azaltarak daha düzgün kesme ve daha uzun takım ömrü sağlar.
- Geliştirilmiş Sertlik: Kaplamalar takımın yüzeyinin sertliğini arttırır, aşınmaya karşı daha dayanıklı hale getirir ve takım ömrünü uzatır.
- Geliştirilmiş Isı Direnci: Kaplamalar, işleme sırasında oluşan yüksek sıcaklıklara dayanabilir, ısıya bağlı takım aşınmasını azaltır ve kesme hızlarını artırır.
- Birikmeyi Önleyici Özellikler: Bazı kaplamalar yapışma önleyici özelliklere sahiptir ve aletin kesici kenarlarında malzeme birikmesini önler.
- Artırılmış Kayganlık: Kaplamalı takımlar daha iyi yağlayıcılığa sahiptir, aşırı kesme sıvısı ihtiyacını azaltır ve talaş tahliyesini artırır.
C. Takım Ömrü ve Aşınma
Takım ömrünü ve aşınmayı anlamak, işleme süreçlerini optimize etmek ve üretim maliyetlerini en aza indirmek için çok önemlidir. Takım ömrü, bir kesici takımın değiştirilmesi veya yenilenmesi gerekmeden önce etkili kaldığı süreyi ifade eder. Takım ömrünü ve aşınmayı çeşitli faktörler etkiler:- kesme Hızı: Daha yüksek kesme hızları, işleme sırasında oluşan daha yüksek sıcaklıklar nedeniyle takım aşınmasının artmasına neden olabilir. Takım ömrünü ve üretkenliği dengelemek için kesme hızlarının doğru seçilmesi çok önemlidir.
- İlerleme hızı: Kesici takımın iş parçasına doğru ilerleme hızı takım aşınmasını etkiler. Yüksek ilerleme hızları aşınmayı hızlandırabilirken, düşük ilerleme hızları takım ömrünü uzatabilir.
- Kesme Derinliği: Kesme derinliği, geçiş başına kaldırılan malzeme miktarını etkiler. Daha derin kesimler takım aşınmasını artırabilir, bu nedenle derinliğin optimize edilmesi kritik öneme sahiptir.
- Malzeme Sertliği: Sert malzemeleri kesmek aletin aşınmasını hızlandırabilir. Sert malzemelerin etkili bir şekilde işlenmesi için özel takımlar ve kaplamalar kullanılır.
- Soğutucu ve Yağlama: Uygun soğutma sıvısı ve yağlama, ısının dağıtılmasına ve sürtünmenin azaltılmasına yardımcı olarak takım ömrünü uzatır.
- Alet Malzemesi: Kesici takımın yapıldığı malzeme aşınma direncini etkiler. Karbür ve seramik gibi malzemeler mükemmel aşınma direnci sunar.
- Takım Geometrisi: Talaş açısı, boşaltma açısı ve talaş kırıcı tasarımı da dahil olmak üzere kesici takımın geometrisi, aşınma modellerinde önemli bir rol oynar.
- İş parçası malzemesi: İşlenen malzemenin türü takım aşınmasını etkiler. Aşındırıcı malzemeler aletin daha hızlı aşınmasına neden olabilir.
Hassas İşleme Süreçleri
Hassas işleme süreçleri, hammaddelerin dar toleranslara ve olağanüstü yüzey kalitesine sahip yüksek hassasiyetli parçalara dönüştürüldüğü yöntemlerdir. Bu bölümde beş temel hassas işleme sürecini inceleyeceğiz: Tornalama, Frezeleme, Delme, Taşlama ve Elektrik Erezyon İşleme (EDM). Bu süreçlerin her biri benzersiz bir amaca hizmet eder ve iş parçasının özel gereksinimlerine göre uygulanır.A. Tornalama
Tornalama, öncelikle silindirik parçaların şekillendirilmesi için kullanılan bir işleme işlemidir. Tek noktalı bir kesici takım malzemeyi dış yüzeyden çıkarırken bir iş parçasının döndürülmesini içerir. Tornalamanın temel yönleri şunlardır:- Silindirik Parçalar: Tornalama, miller, pimler ve manşonlar gibi silindirik bileşenlerin üretimi için idealdir.
- Dönme Simetrisi: İş parçası bir torna tezgahında dönerken kesici takım onu şekillendirdiğinden, dönme simetrisi gerektiren parçalar için çok uygundur.
- Çeşitli Operasyonlar: Tornalama, yüz tornalama, tornalama (çapın küçültülmesi), konik tornalama ve diş açma dahil olmak üzere çeşitli işlemleri gerçekleştirebilir.
- Tek Noktada Kesim: Tek bir kesme takımı, malzemeyi sürekli bir hareketle kaldırarak verimli malzeme çıkarma işlemi sağlar.
- Torna Makineleri: Tornalama işlemlerinde yaygın olarak hem manuel hem de CNC kontrollü torna tezgahları kullanılmaktadır.
B. Frezeleme
Frezeleme, iş parçasından malzemeyi çıkarmak için çok noktalı kesici takımların kullanıldığı çok yönlü, hassas bir işleme işlemidir. Çok çeşitli şekil ve özellikler oluşturmak için çok uygundur. Frezelemenin temel yönleri şunlardır:- Çok yönlülük: Frezeleme düz yüzeyler, yuvalar, cepler ve karmaşık konturlar üretebilir. Hem 2D hem de 3D işleme için kullanılır.
- Çok Noktalı Kesim: Takım üzerindeki birden fazla kesme kenarı, iş parçasıyla aynı anda etkileşime girerek verimli talaş kaldırma işlemine olanak tanır.
- Freze Çeşitleri: Frezeleme, parmak frezeler, yüzey frezeleri ve bilyalı değirmenler dahil olmak üzere çeşitli tipte kesiciler kullanılarak gerçekleştirilebilir.
- CNC İşleme Merkezleri: CNC kontrollü freze makineleri, takım hareketi üzerinde hassas kontrol sağlar ve modern işlemede yaygın olarak kullanılır.
- Yüksek Hızlar: Frezeleme yüksek hızlarda yapılarak verimli üretim yapılabilir.
C. Delme
Delme, iş parçalarında delik oluşturmak için kullanılan hassas bir işleme işlemidir. Çeşitli sektörlerde temel bir operasyondur. Sondajın temel yönleri şunları içerir:- Delik Oluşturma: Delme makineleri, malzemeyi çıkarmak ve belirli çaplarda delikler oluşturmak için matkap adı verilen özel aletler kullanır.
- Matkap Çeşitleri: Her biri özel uygulamalar için tasarlanmış, bükümlü matkaplar, puntalı matkaplar ve değiştirilebilir matkaplar dahil olmak üzere farklı tipte matkaplar mevcuttur.
- doğruluk: Deliklerin doğru şekilde oluşturulmasını sağlamak için delme işleminde hassas konumlandırma ve hizalama çok önemlidir.
- Hız ve İlerleme Hızı: Dönme hızı ve ilerleme hızı gibi delme parametreleri, istenen delik boyutlarına ulaşmak için kritik öneme sahiptir.
- Soğutucu ve Yağlama: Delme sırasında ısıyı dağıtmak ve sürtünmeyi azaltmak için uygun soğutucu ve yağlama kullanılır.
D. Taşlama
Taşlama, malzemeyi çıkarmak ve son derece dar toleranslar ve yüzey kalitesi elde etmek için aşındırıcı tekerlekler kullanan hassas bir işleme işlemidir. Öğütmenin temel yönleri şunları içerir:- Olağanüstü Hassasiyet: Taşlama mikron düzeyinde hassasiyete ulaşabilir, bu da onu en yüksek doğruluk gerektiren uygulamalar için ideal kılar.
- yüzey: Üstün yüzey kalitesi sağlar ve çoğu zaman ek sonlandırma işlemlerine olan ihtiyacı ortadan kaldırır.
- Malzemeler: Taşlama, sertleştirilmiş çelik, seramik ve karbürler dahil olmak üzere sert ve aşındırıcı malzemeler için uygundur.
- Çeşitli Taşlama Yöntemleri: Yüzey taşlama makineleri, silindirik taşlama makineleri ve puntasız taşlama makineleri gibi farklı taşlama makineleri türleri, çeşitli işleme ihtiyaçlarını karşılar.
- Soğutucu: Taşlama sırasında aşırı ısınmayı önlemek ve taş bütünlüğünü korumak için uygun soğutma sıvısı şarttır.
E. Elektrik Boşaltma İşleme (EDM)
EDM veya Elektrik Erozyon İşleme, malzemeyi çıkarmak için elektrik deşarjlarını kullanan, geleneksel olmayan hassas bir işleme işlemidir. Özellikle karmaşık ve karmaşık şekillerin yanı sıra sert ve ısıya dayanıklı malzemelerin işlenmesi için uygundur. EDM'nin temel yönleri şunları içerir:- Temassız İşleme: EDM, takım ile iş parçası arasında doğrudan teması gerektirmez, bu da takımın aşınma ve hasar riskini azaltır.
- Yüksek Hassasiyetli: EDM yüksek hassasiyete ulaşabilir, bu da onu dar toleransların gerekli olduğu uygulamalar için uygun hale getirir.
- Karmaşık Şekiller: Karmaşık şekillerin, kalıpların, kalıpların ve ince detaylara sahip bileşenlerin işlenmesinde mükemmeldir.
- Tel Erozyon ve Sinker Erozyon: EDM makinelerinin iki temel türü vardır: tel elektrot kullanan tel EDM ve şekillendirilmiş elektrot kullanan platin EDM.
- Yavaş Süreç: EDM, diğer işleme yöntemleriyle karşılaştırıldığında nispeten yavaştır; bu da onu düşük adetli, yüksek hassasiyetli işler için en uygun hale getirir.
Toleranslar ve Kalite Kontrol
Hassas işleme, parçaların belirtilen standartları karşıladığından emin olmak için ayrıntılara titizlikle dikkat edilmesini ve kalite kontrolüne sıkı bir bağlılık gerektirir. Bu bölümde hassas işlemede kalite kontrolün üç kritik yönünü inceleyeceğiz: Geometrik Boyutlandırma ve Tolerans (GD&T), İstatistiksel Proses Kontrolü (SPC) ve Kalite Güvencesi.A. Geometrik Boyutlandırma ve Toleranslandırma (GD&T)
Genellikle GD&T olarak kısaltılan Geometrik Boyutlandırma ve Toleranslama, bir parça üzerindeki özelliklerin boyut, form, yönelim ve konumunda izin verilen varyasyonları tanımlamak ve iletmek için kullanılan bir sistemdir. GD&T aşağıdaki nedenlerden dolayı hassas işlemede hayati öneme sahiptir:- Hassas İletişim: GD&T, mühendislerin, tasarımcıların ve makinistlerin tasarım amacını ve boyutsal gereksinimleri doğru bir şekilde iletmeleri için standartlaştırılmış bir dil sağlar.
- Tolerans Açıklaması: Kritik boyutlardaki kabul edilebilir varyasyonun tanımlanmasına yardımcı olarak tüm paydaşların izin verilen sapmaları anlamasını sağlar.
- Geliştirilmiş Kalite: GD&T, tasarım özelliklerindeki belirsizliği azaltarak, işleme sırasında hata riskini en aza indirerek kalitenin iyileştirilmesini destekler.
- Maliyet Verimliliği: Açık GD&T spesifikasyonları, yanlış anlama veya yanlış yorumlama nedeniyle parçaların hurdaya çıkma veya yeniden işleme gerektirme olasılığı daha düşük olduğundan, üretim maliyetlerinin azalmasına yol açabilir.
- Karmaşık Geometri: Özellikle karmaşık geometriye sahip parçalar için kullanışlıdır ve tüm özelliklerin istenilen özelliklerde üretilmesini sağlar.
B. İstatistiksel Süreç Kontrolü (SPC)
İstatistiksel Süreç Kontrolü (SPC), işleme sürecini izlemek ve kontrol etmek için istatistiksel teknikleri kullanan bir kalite kontrol metodolojisidir. SPC, hassas işlemede aşağıdaki nedenlerden dolayı önemlidir:- Süreç İzleme: SPC, işleme proseslerinin gerçek zamanlı olarak izlenmesine, istenen parametrelerdeki varyasyonların veya sapmaların belirlenmesine yardımcı olur.
- Sorunların Erken Tespiti: SPC, prosesi sürekli izleyerek, spesifikasyon dışı parçalara yol açabilecek sorunların erken tespitine olanak tanır, israfı ve yeniden çalışmayı azaltır.
- Veriye Dayalı Karar Verme: SPC, işleme sürecinin kabul edilebilir sınırlar içinde kalmasını sağlayarak süreç ayarlamaları hakkında bilinçli kararlar vermek için verilere ve istatistiksel analizlere güvenir.
- Geliştirilmiş Tutarlılık: SPC proses tutarlılığını destekler ve uygun olmayan parçaların üretilmesi olasılığını azaltır.
- Daha Az Hurda ve Yeniden İşleme: SPC, süreç değişikliklerini anında tanımlayıp ele alarak hatalı parçaların üretimini en aza indirir, hurda ve yeniden işleme maliyetlerini azaltır.
C. Hassas İşlemede Kalite Güvencesi
Hassas işlemede kalite güvencesi, üretilen parçaların belirlenen kalite standartlarını karşılamasını veya aşmasını sağlamaya yönelik kapsamlı bir yaklaşımı kapsar. Aşağıdakiler de dahil olmak üzere çeşitli unsurları içerir:- Süreç Dokümantasyonu: Standart işletim prosedürleri (SOP'ler) ve çalışma talimatları dahil olmak üzere işleme süreçlerinin ayrıntılı belgelenmesi, her adımın tutarlı bir şekilde gerçekleştirilmesini sağlar.
- Muayene ve Ölçüm: Hassas aletler ve metroloji teknikleri kullanılarak yapılan titiz inceleme ve ölçümler, parçaların belirtilen toleranslara ve kalite standartlarına uygun olduğunu doğrular.
- ayarlama: Doğruluğu ve izlenebilirliği korumak için işleme ekipmanının ve ölçüm cihazlarının düzenli kalibrasyonu önemlidir.
- Malzeme Doğrulaması: Kullanılan malzemenin tasarım gereksinimlerini karşıladığından emin olmak için malzeme özelliklerinin, bileşiminin ve kalitesinin doğrulanması kritik öneme sahiptir.
- Çalışan eğitimi: Makinistlere ve kalite kontrol personeline yönelik eğitim ve beceri geliştirme programları, onların rol ve sorumluluklarında yetkin olmalarını sağlar.
- Sorun kaynağı çözümlemesi: Uygun olmayan parçalar tespit edildiğinde sorunun kaynağının tespit edilmesi ve düzeltici aksiyonların alınması için kök neden analizi yapılır.
- Sürekli İyileştirme: Sürekli iyileştirme kültürü, yeniliği teşvik eder ve işleme süreçlerinde ve kalite kontrol prosedürlerinde sürekli iyileştirmelere yön verir.
- Müşteri Görüşleri: Müşteri geri bildirimlerinin toplanması ve analiz edilmesi, iyileştirilecek alanların belirlenmesine yardımcı olur ve işleme süreçlerini müşteri beklentileriyle uyumlu hale getirir.
Sonuç
A. Hassas İşleme Sanatı ve Bilimi
Hassas işleme, yaratıcılığın, becerinin ve yeniliğin endüstrileri yönlendiren ve modern dünyayı şekillendiren yüksek hassasiyetli parçalar üretmek için birleştiği sanat ve bilimin kesişim noktasında yer almaktadır. Hem ham maddeleri mükemmel mühendislik eserlerine dönüştüren makinistlerin ustalığını ve uzmanlığını gerektiren bir sanat formudur, hem de benzersiz hassasiyet elde etmek için en son teknolojiye, malzeme bilimine ve gelişmiş süreçlere dayanan bir bilimdir. Hassas işleme yolculuğu, bizi malzemeleri ve bunların özelliklerini anlama, kesici takımlar ve makinelerdeki ustalık ve süreç ve toleransların titizlikle kontrol edilmesi aşamalarından geçirir. Geometrik boyutlandırma ve tolerans dilini, istatistiksel süreç kontrolünün dikkatliliğini ve kalite güvencesine bağlılığı kapsar. Hassas işleme, havacılık ve otomotivden tıbbi cihazlara ve elektroniğe kadar çeşitli endüstrilerde, uçak motorlarından yapay eklemlere ve mikroçiplere kadar her şeyin şekillendirilmesinde önemli bir rol oynamaktadır. Eşsiz doğruluk ve güvenilirlikle çalışan, genellikle mümkün olanın sınırlarını zorlayan bileşenlerin oluşturulmasına olanak tanır.B. Son Düşünceler
Hassas işleme konusundaki bu araştırmamızı tamamladığımızda, bu alanın yalnızca parçaların oluşturulmasıyla ilgili olmadığı açıktır; olasılıkların yaratılmasıyla ilgilidir. Hassasiyet arayışı, yeniliği teşvik ederek, başarılabileceklerin sınırlarını zorlar. İster bir saatin karmaşık dişlilerini oluşturmak için gereken hassas işçilik, ister karmaşık havacılık ve uzay bileşenleri üretmek için gereken ileri teknoloji olsun, hassas işleme her şeyin merkezinde yer alır. Hassas işlemenin geleceği umut vericidir. Malzeme bilimi, otomasyon ve dijital teknolojilerdeki ilerlemeler manzarayı yeniden şekillendirmeye devam ediyor. Minyatürleştirme, 3 boyutlu baskı ve sürdürülebilir üretim uygulamaları giderek daha fazla öne çıkıyor ve sektöre yeni ufuklar açıyor. Hassasiyetin her zamankinden daha önemli olduğu bir dünyada hassas işleme, modern mühendisliğin vazgeçilmez bir dayanağı olmaya devam ediyor. Bu, insan yaratıcılığının ve imalatın her alanında yılmaz mükemmellik arayışımızın bir kanıtıdır. Daha yüksek hassasiyete ve daha karmaşık bileşenlere olan talep arttıkça, hassas işleme gelişmeye devam edecek ve yarının zorluklarını yüzyıllardır tanımlayan kararlılık ve hassasiyetle karşılayacaktır.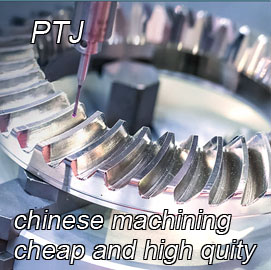
Hizmetlerimiz
- 5 Eksen İşleme
- Cnc Frezeleme
- Cnc Tornalama
- İşleme Endüstrileri
- Işleme süreci
- Yüzey İşlem
- Metal İşleme
- Plastik İşleme
- Toz Metalurji Kalıbı
- Döküm Döküm
- Parça Galerisi
Durum çalışmaları
- Oto Metal Parçaları
- Makine parçaları
- LED Soğutucu
- Yapı Parçaları
- Mobil Parçalar
- Tıbbi Parçalar
- Elektronik parçalar
- Özel İşleme
- Bisiklet Parçaları
Malzeme listesi
- Alüminyum İşleme
- titanyum işleme
- Paslanmaz Çelik İşleme
- Bakır İşleme
- Pirinç İşleme
- Süper Alaşımlı İşleme
- Peek İşleme
- UHMW İşleme
- Unilate İşleme
- PA6 İşleme
- PPS İşleme
- Teflon İşleme
- İnkonel İşleme
- Takım Çeliği İşleme
- Daha Fazla Malzeme
Parça Galerisi